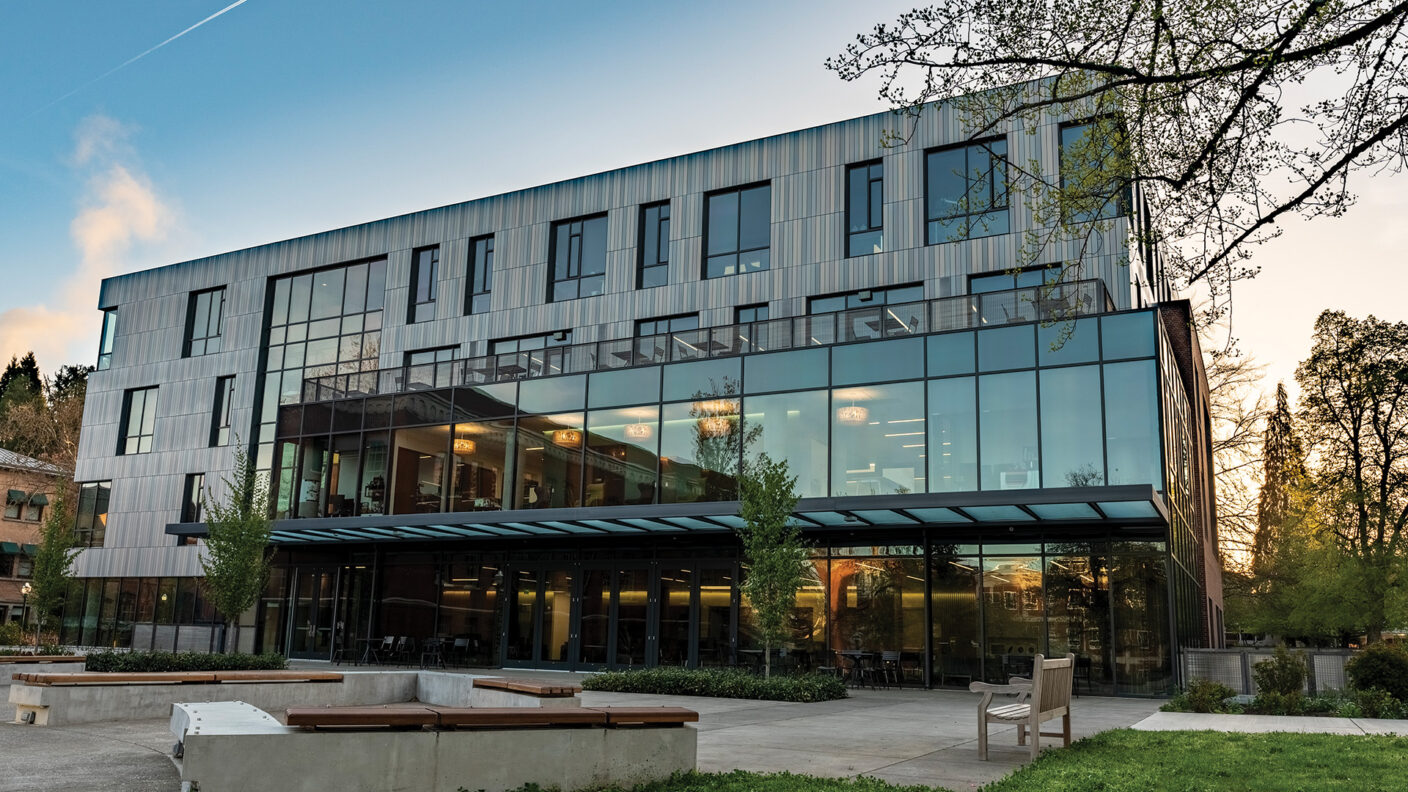
- 63,000 square feet
- LEED Gold certification
- Meets Architecture 2030 Challenge goals
University of Oregon Tykeson Hall
High Standard of Success
Situated in the heart of campus and home to the University of Oregon’s College of Arts and Sciences, Tykeson Hall was intended to serve as a campus destination, reinforcing a sense of community with an environmentally conscious mission. The design achieved LEED v4 Gold certification and meets the stringent goals of the Architecture 2030 challenge.
Tykeson Hall is one of the first buildings in the Pacific Northwest to integrate post-tensioned concrete slab construction with high-efficiency radiant heating and cooling floors. The high-performance building thermal envelope with extensive exposed thermal mass is served by in-floor hydronic systems that minimize interior temperature swings. The building also features two heat recovery air handler units, all outside air, and no recirculation to provide exceptional air quality throughout, supplied through active chilled beams.
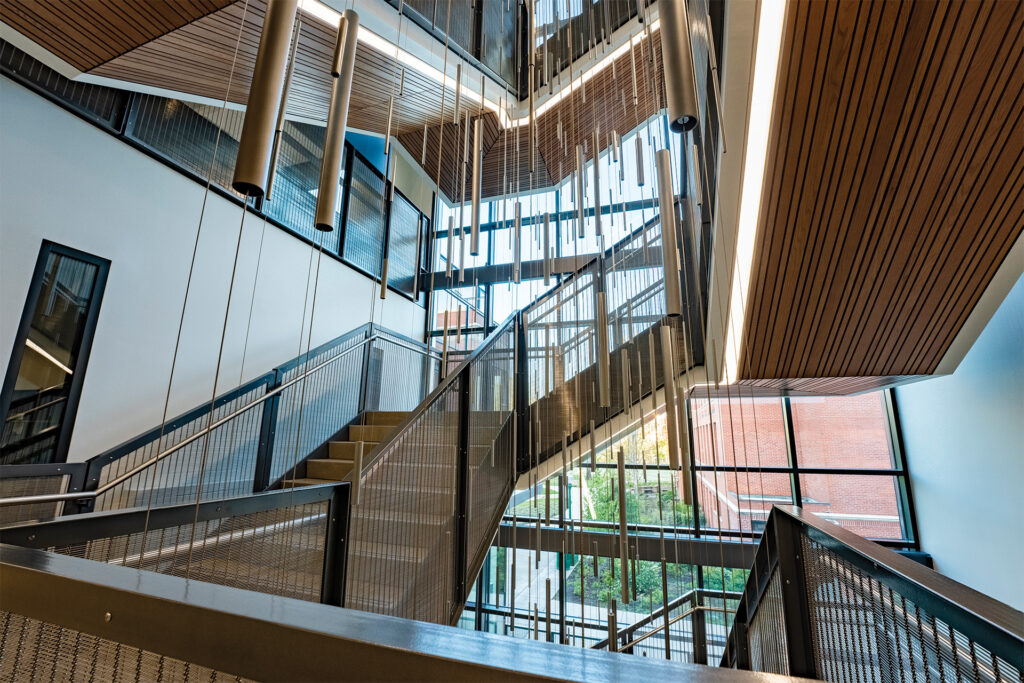
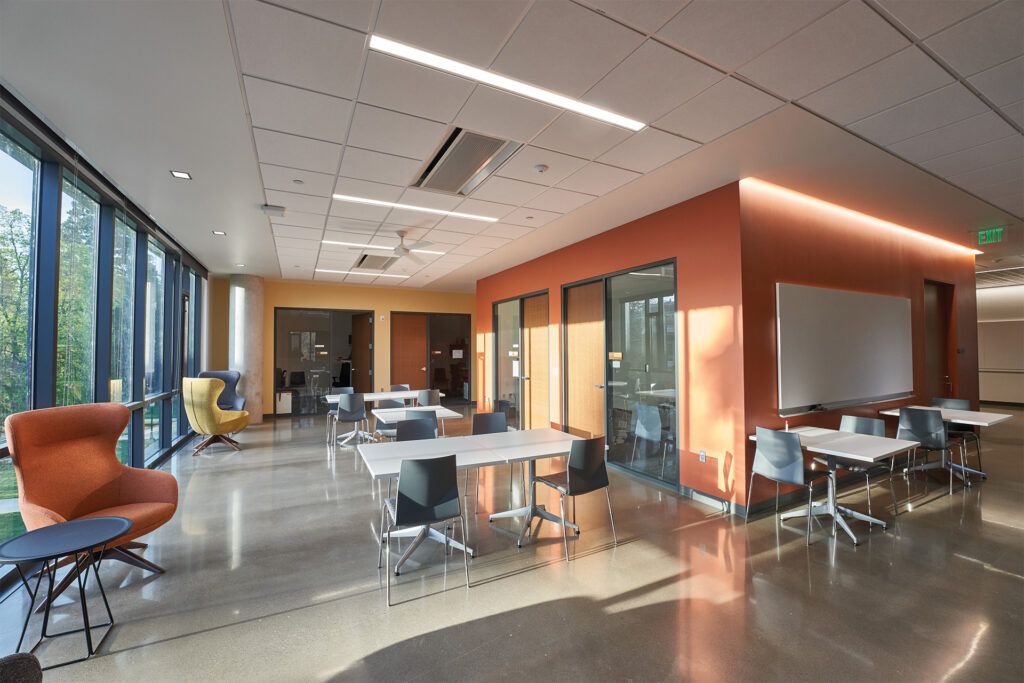

System Optimization
Tykeson Hall was a seamless collaboration between all parties, allowing for a well-executed project with very few requests for information (RFIs).
Owner energy savings goals required us to achieve specific methodologies and extensive system design requirements. We leveraged a cooling design strategy using higher temperature campus return water to meet requirements without adding to the overall campus flow demand. Our design improved the campus chilled water operation, which was frequently experiencing ‘low delta T syndrome,’ moving more water than could be used for cooling requirements.
We introduced multiple cooling coils to provide dehumidification when needed, without the use of face and bypass dampers in air handlers. We also used ceiling fans to provide local air movement to increase the comfort of the building during heating and cooling, while also adding interesting visual elements to the space.
Early on in the project we realized that in order to achieve optimal energy savings, the systems should be dormant when the building was unoccupied. We automated the system starting times separately for heating and cooling requirements so that the optimal building temperatures were reached prior to occupancy schedule. To do this, we used occupancy sensors extensively to inform temperature setbacks and lighting timing.
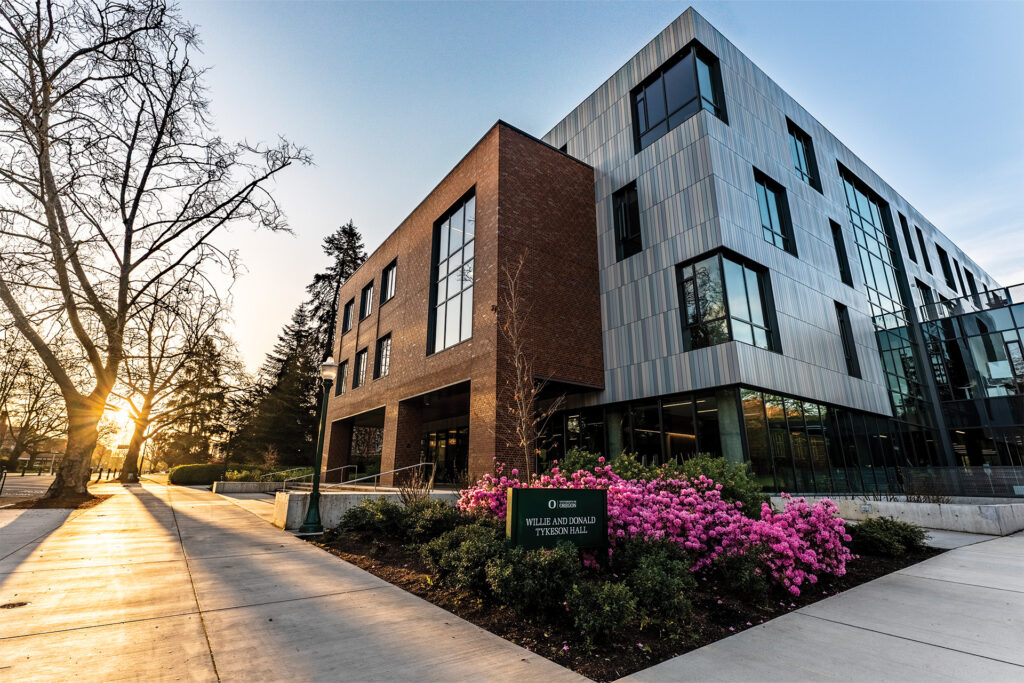
Elevating Building Performance
Our team rose to the challenge for this project, executing on a design that provided optimal energy savings and occupant comfort from initial operation. In addition to being LEED- Gold certified, the building performed at a 47% reduction in energy cost savings due to the highly efficient chilled water and combined heat and power system, heat recovery, LED lighting, daylight sensors, and thermal assembly. Added sustainability elements include a 38% reduction of indoor water use for low-flow fixtures and 62,500 gallons of water saved annually on irrigation using an efficient drip system with drought tolerant plantings.
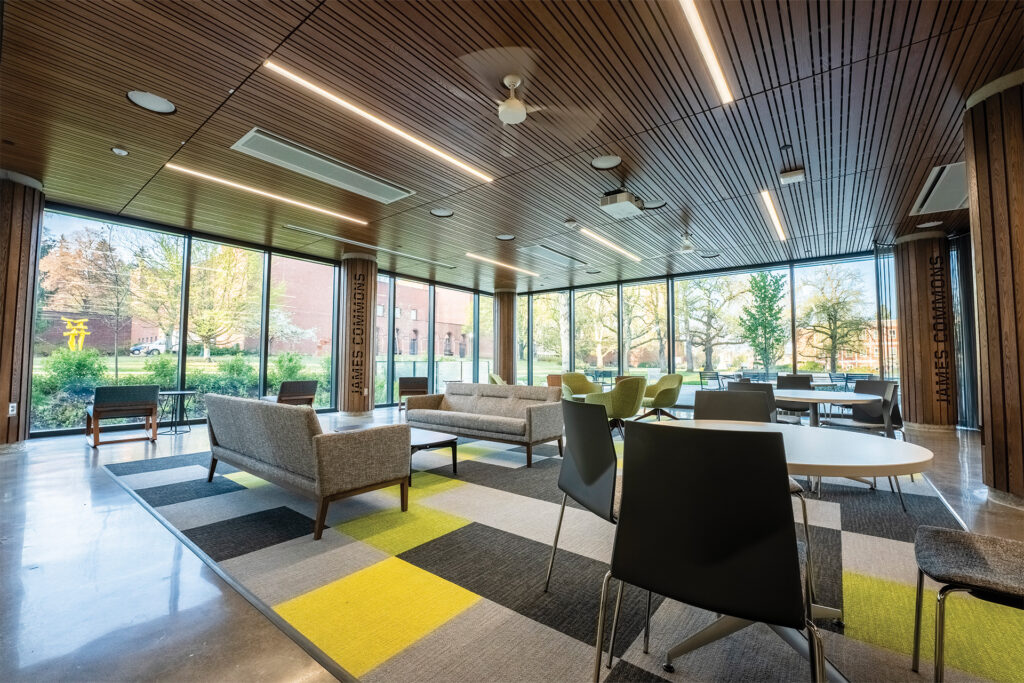
Want to be a part of projects like this? Join Our Team.